Cost estimation: What do I need for a reliable cost forecast?
It is not only in major projects such as the Berlin Airport that costs get out of control. Every day, the cost framework of projects in companies is sometimes dramatically exceeded. Cost estimation or cost determination therefore plays a central role in project management. It is a decisive factor in whether or not a project or contract can be completed successfully. The goal must therefore be to determine the expected costs and value of a product in advance as accurately as possible to weigh up the risks. Various tools are available in business practice for this purpose.
What exactly defines the terms such as cost estimation, cost determination, cost calculation, production costs, planned costs and actual costs? How can anticipated production costs be predicted with reasonable effort, a cost breakdown into cost groups and the necessary precision? In this article we will address and give you answers to these questions.
What is cost estimation?
Basically, the term cost estimation in a business sense describes the forecast of costs incurred by a company, a product, a service or a project. Whenever costs cannot be planned exactly, at least an effort estimate must be made. This allows to roughly determine whether an order or a project can be economically realised at all. Unprofitable projects can also be prevented in this manner or stopped in time. A good cost estimate or cost determination is in addition a basis for viable business cases.
Especially in project management, cost estimation is a central challenge, since projects by definition alone deal with the realisation of something new. Cost estimation is simplified on the one hand by past experience and on the other hand by a well-organised knowledge database. If empirical values from past projects are systematically available as a basis, planning becomes much more convenient and accurate. In addition to personnel costs and material costs, which are naturally the largest cost group, some other items and fundamentals should not be forgotten. For example, travel costs, costs for external consultants or licences, financing costs, infrastructure costs and provisions for unforeseeable expenses should also be mentioned.
In practice, various methods have become established as the basis for cost estimation. These include the less complex top-down approach and the much more complex but more detailed bottom-up approach. For large-scale projects, so-called estimation meetings are also used.
Cost estimation according to the top-down approach
In this top-down approach, a ballpark estimate of the total costs is initially made on the basis of known reference values. In other words, a lump-sum budget is set based on empirical values, to which the project team must then orient itself in the conduction course of the project. Individual budgets for work packages or sub-projects are derived from the overall budget. The procedure is appealing because of its simplicity, but it has the disadvantage that a certain degree of imprecision cannot be ruled out due to a still uncertain framework condition. Sometimes, however, a certain cost pressure is also intended in order to set clear limits right from the very beginning.
Cost estimation according to the bottom-up approach
The bottom-up approach causes a significantly higher effort than the top-down approach. Based on the detailed planning, all steps within the defined work packages are evaluated. For each point, it must be clarified how long the implementation will take and what resources are required. Special project management software is often nowadays used to make the complexity more manageable.
The advantage of this approach is that the technical knowledge of those responsible for the work packages can be incorporated. In some cases, however, those who are responsible plan generously in order to survive reductions, which is why there must be a certain sense of responsibility on the part of those involved. In addition, the individual estimates must always be critically scrutinised.
Estimation workshop
The estimation workshop has some similarities with the bottom-up approach. However, in an estimation workshop, planned work packages are evaluated by independent experts. These experts supply their estimate concealed and without prior discussion. This is followed by a summary of the results and a statistical evaluation. If there are clear identifiable outliers, these are discussed. New evaluations are conducted until there is agreement.
The advantage of this method is that the results are more accurate. In addition, alternative solutions are often developed that allow a more cost-effective project implementation. Due to the high effort involved, this method is usually only used on large projects.
What costs are included in production costs?
The term “production costs” refers to all costs incurred in the production of a product. Basically, the following types of costs are included in manufacturing costs:
- Material input costs (raw materials, auxiliary materials, operating materials)
- Material overheads (e.g., warehousing costs, transport costs)
- Direct production costs (wages)
- Production overheads (e.g., costs of the production facility)
- Special direct costs of production
- External services
If these costs are added up, this results in the production costs that must be capitalised (lower value limit). Optionally, the following costs can be added:
- Administrative overheads
- Expenses for social facilities
- Expenses for voluntary social benefits
- Expenses for company pension schemes
- Interest on borrowed capital (under certain conditions)
The result of adding these cost types is the so-called capitalizable production costs (upper value limit).
What are planned costs?
Planned costs are the planned or estimated costs for future periods. On the one hand, they serve as a standard value, on the other hand, they also serve as a comparative value. In principle, planned costs arise under the assumption that defined services are provided under defined conditions. A simple example is the manufacture of a product in a certain quantity and at certain conditions. Simplified put, a distinction can be made between two methods:
- Fixed standard costing
- Flexible standard costing
Let us take a closer look at these two variants in the following.
Fixed standard costing
Fixed budgeted costing is the simplest form of budgeted costing. The simplification arises in particular from the fact that the planned costs are calculated with an operating level that is fixed for a period. This means that no distinction is made between fixed and variable costs. Both direct and overhead costs are included.
The process is as follows: The first step is to determine the direct costs per cost centre or cost unit. Following by, the overhead costs are determined. This is only possible if the company has cost centres for the clear allocation of overhead costs. In planning, a certain capacity utilisation (a fixed capacity utilisation) is then assumed. Reference values must therefore be defined that are in a proportional relationship with the planned cost types:
- Direct reference values (e.g., quantities, production times)
- Indirect reference values (overhead rates for cost centres without direct activity reference)
- Alternative: Lump sum standard values
Now the plan utilisation is defined. It is equal to the activity over which the total costs will be distributed in the plan period. Subsequently, the total plan costs are divided by the plan employment. This results in the so-called standard cost rate – i.e., the costs per unit of activity.
Flexible standard costing
Unlike Fixed budgeted costing, flexible budgeted costing allows for effective cost control. The reason: by differentiating between fixed and variable costs, it is possible to map different levels of utilisation. The assumption is made that fixed costs remain unchanged, while variable costs develop proportionally to utilisation (employment). Variable and fixed costs are separated at the cost centre level.
The main advantage of this alternative is that it facilitates an investigation into the causes of deviations between target and actual costs. The following types of deviation can be identified:
- Consumption variance: Arises, for example, due to high waste or high consumption of operating resources
- Operating variance: Usually due to unused capacities (so-called idle costs); indicates an over- or under-coverage of planned fixed costs
- Alternative: Flat-rate standard value price variance (occurs, for example, due to a short-term price increase in purchasing)
- Total variance: Shows whether there is an overall cost over-recovery or a cost under-recovery
What are actual costs?
Actual costs are costs that were actually incurred in the past. They are used in cost accounting. Actual costs can be calculated by multiplying actual quantities (quantities actually consumed) by actual prices (procurement or acquisition prices, production costs). If cost and activity accounting in a company only considers actual costs, this is called actual cost accounting. This is a purely past-related approach in which all special effects and irregularities are included in fully in the actual costs.
Actual cost accounting provides some important information about the profitability of a company. It enables the presentation of absolute and percentage changes in a time period comparison or on a project schedule. It can also be used for post-cost calculation and pricing control. It is also used for inventory valuation on the basis of production costs for the balance sheet. As a traditional form of cost accounting, it requires little effort, as controlling can take most of the data directly from financial accounting. However, its informative value is limited, since it is a purely past-related observation. There is therefore no comparison of target and actual values.
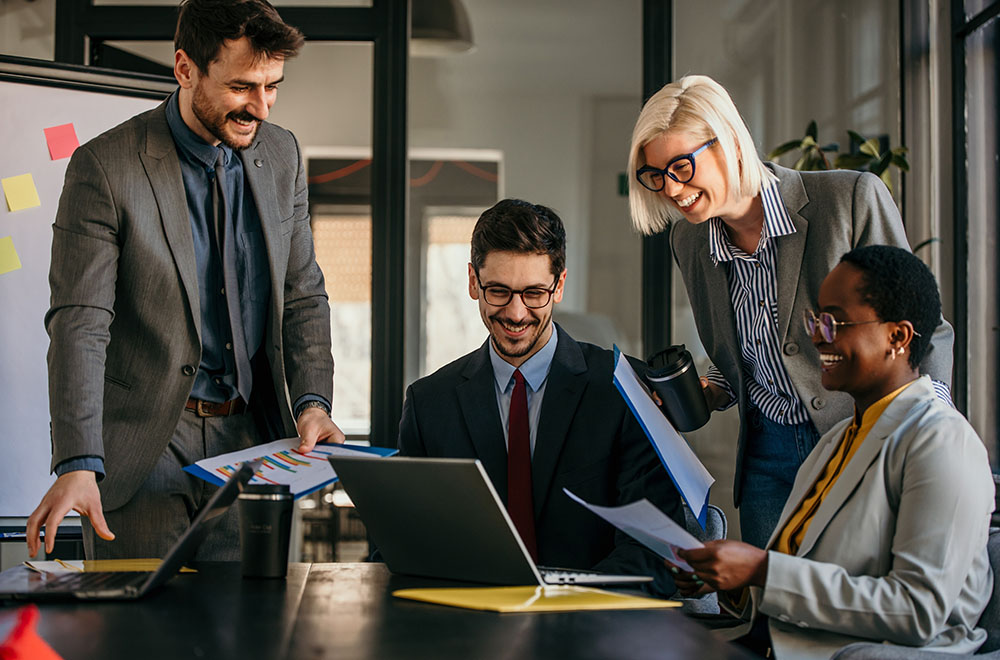
Reliable cost estimate with 4cost
The software and service solutions from 4cost provide you with a maximum of cost transparency at all phases. For improved cost control and increased profitability.
Request a commitment-free presentation now. Our experts will be happy to advise you on the right solutions for your company.