Choosing the right costing strategy: Bottom-up or top-down?
In the dynamic world of business, effective cost management is pivotal for sustainability and growth. The ability to accurately estimate and control costs can be the difference between profit and loss, making it a critical factor in strategic planning and decision-making. Amidst various costing methodologies, two distinct approaches stand out: bottom-up and top-down costing.
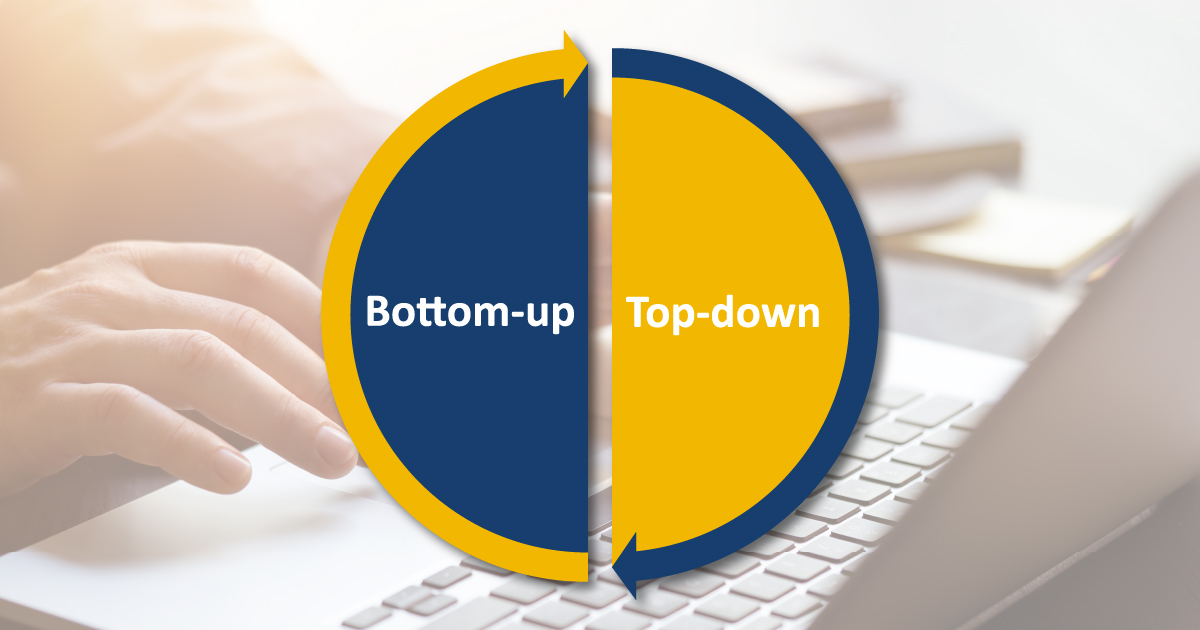
Bottom-up costing is a meticulous approach that starts at the most fundamental level, building cost estimates from the ground up. It involves analysing individual components of a project or product, assessing their costs, and then aggregating these to form a total cost estimate. This method is known for its detail-oriented nature, providing a granular view of where every penny is spent.
On the other hand, top-down costing takes a broader view. It begins with a macro-level estimate of the total cost, often based on historical data and strategic objectives, and then allocates portions of this total to various components or departments. This approach is generally quicker and less detailed than the bottom-up method, offering a more strategic, big-picture view of costs.
Understanding the nuances of bottom-up and top-down costing is crucial for businesses to make informed decisions that align with their financial and operational goals. This post deals with the principles of both approaches and is a helpful guide to choosing the right costing strategy.
Understanding bottom-up costing
Definition and explanation of bottom-up costing
Bottom-up costing is a comprehensive approach to estimating costs that begins at the most granular level. In this methodology, costs are calculated for each individual component or activity involved in a project or production process. These individual cost elements are then cumulatively added to arrive at the total cost estimate. This method is grounded in the principle that a precise understanding of each part leads to an accurate picture of the whole.
Key components and implementation
Identification of components: The first step is to identify all the components or activities involved in a project or production process.
Detailed cost assessment: For each identified component, a detailed analysis of the cost is conducted. This can include material costs, labour costs (man and machine), overheads, and any other direct or indirect costs.
Aggregation of costs: After assessing the costs of each component, these are aggregated to form the overall project or product cost.
Continuous updating: As the project progresses, the cost estimates are regularly updated to reflect any changes or new insights.
Advantages of bottom-up costing
Attention to detail: As every component and every work step is taken into account, this approach tends to be more accurate and realistic.
Flexibility in planning: The approach allows for a more flexible approach to budgeting and planning, as each element can be adjusted individually.
Enhanced control: By understanding the cost implications of each component, managers can exert better control over the budget.
Potential drawbacks
Time-consuming: The detailed nature of this method can make it quite time-intensive, especially for large projects with numerous components.
Complexity: The level of detail required can lead to complexity in cost management and analysis.
Risk of overemphasis on minor costs: There's a possibility of focusing too much on small costs, potentially overlooking the bigger picture.
In conclusion, bottom-up costing is a detailed, meticulous approach that offers high accuracy but can be time-consuming and complex. It is often preferred in scenarios where precision in cost estimation is paramount, and the scope for error needs to be minimal.
Understanding top-down costing
Definition and explanation of top-down costing
Top-down costing is a strategic approach to estimating costs that starts at the highest level. In contrast to bottom-up costing, this method begins with a macro estimate of the total project or product cost, often based on historical data, industry benchmarks, or strategic goals. From this overarching estimate, costs are then allocated to various components or departments of the project. This approach is characterized by its emphasis on the big picture, prioritizing speed and simplicity over minute details.
Key components and implementation
Establishing an overall budget: The process starts by defining an overall budget for the project or product, based on strategic objectives or historical data.
Allocation of budget: This total budget is then distributed across various components or departments, often proportionally or based on historical spending patterns.
Top-level adjustments: As the project progresses, adjustments are made at the top level, with changes trickling down to individual components.
Monitoring and control: Regular monitoring is conducted to ensure that spending aligns with the top-down budget allocations.
Advantages of top-down costing
Time-efficient: This approach is generally quicker to implement than bottom-up costing, making it suitable for tight deadlines.
Easier to implement: It requires less detailed data collection and analysis, which simplifies the costing process.
Strategic focus: Top-down costing aligns well with strategic objectives and can be effectively used in high-level decision making.
Possible limitations
Less accuracy: The lack of detailed analysis can lead to less accurate cost estimates, especially for complex projects.
Potential for budget overruns: Without detailed component-level insights, there is a risk of underestimating costs, leading to budget overruns.
Inflexibility in handling changes: Adjustments in one area might require extensive reallocation across the entire budget, making it less flexible in response to changes.
In summary, top-down costing is a strategic, high-level approach that offers speed and simplicity but may compromise on accuracy and detail. It is often favoured in situations where quick decision-making is required, and the company has a solid historical database to rely on for initial estimates.
Comparative analysis
The choice between Bottom-Up and Top-Down Costing approaches can significantly impact a business's project management and financial planning. Understanding the nuances of each method is crucial for selecting the right approach for a specific scenario.
Direct comparison of bottom-up vs. top-down costing
Detail orientation: Bottom-up costing is more detailed and granular, focusing on individual components, while top-down costing provides a broader, less detailed overview, starting from a macro perspective.
Accuracy: Bottom-up tends to be more accurate due to its detailed nature, whereas top-down may sacrifice some accuracy for speed and simplicity.
Time and resources: Bottom-up requires more time and resources for data collection and analysis, making it more labour-intensive. Top-down is quicker and less resource-intensive.
Flexibility: Bottom-up offers more flexibility in adjusting individual components of the project, while top-down is less flexible in adjusting to changes at the micro level.
Easy implementation: Top-down is generally easier and faster to implement, especially in early planning stages or for initial estimations.
Scenarios where each method is most effective
Bottom-up costing is most effective in:
- Projects where accuracy in cost estimation is critical
- New projects without historical reference data, but with known technologies
- Situations where detailed cost control and monitoring are necessary
Top-down costing is most effective in:
- Early-stage project planning when detailed information is not yet available
- Projects that are similar to previous initiatives with available historical cost data
- Situations requiring quick, strategic decision-making
In conclusion, the choice between bottom-up and top-down costing depends on various factors, including the nature of the project, the need for accuracy, resource availability, and the strategic objectives of the business. Understanding the strengths and limitations of each method allows businesses to make informed decisions that best suit their specific circumstances.
Combining bottom-up and top-down costing
While bottom-up and top-down costing are often viewed as distinct methodologies, integrating these approaches can offer businesses the best of both worlds. This hybrid model harnesses the detailed accuracy of bottom-up costing and the strategic simplicity of top-down costing, creating a more balanced and versatile costing strategy.
Benefits of combining both approaches
Balanced accuracy and efficiency: Combining these methods allows businesses to maintain a high level of cost accuracy without compromising on efficiency and strategic alignment.
Increased flexibility: An integrated approach provides the flexibility to adjust to project changes at both the micro and macro levels.
Improved budget control: It allows for detailed cost control at the component level while aligning with the overall strategic budget set by the top-down approach.
Examples of hybrid models in practice
Phased implementation: In this model, a project starts with a top-down approach to establish an overall budget and then switches to a bottom-up approach for detailed costing as more information becomes available.
Strategic top-down with operational bottom-up: Strategic decisions and budget allocations are made using a top-down approach, while the operational aspects, such as production or project execution, utilise bottom-up costing for detailed financial management.
Iterative alignment: Regularly scheduled coordination meetings are held to align the detailed bottom-up cost data with the top-down budgetary constraints, ensuring both accuracy and strategic alignment.
Recommendations for businesses considering a hybrid model
Assess project needs: Evaluate the nature and requirements of the project to determine the appropriate balance between bottom-up and top-down elements.
Establish clear processes: Define clear processes and checkpoints for when and how the two approaches should interact and integrate.
Training and communication: Ensure that all team members understand both approaches and how they are integrated, promoting effective communication and collaboration.
Regular reviews: Implement regular review sessions to assess the effectiveness of the integrated approach and make adjustments as necessary.
Use specialised software: Utilise software and tools that can support both costing methodologies, allowing for seamless integration and analysis.
Hybrid costing with 4cost costing software
4cost offers globally unique costing software that links both calculation methodologies bidirectionally. This means that all costing data can be transferred back and forth between top-down and bottom-up as required. Depending on the project status and requirements, the advantages of the respective costing model are fully utilised. Top-down for quick cost indications, reliable should cost analyses and fast decisions in early phases, when often only limited information, sketches or specifications are available. Bottom-up for detailed analyses of cost structures and different scenarios in later phases with a higher level of information. Seamless data exchange between top-down and bottom-up guarantees a consistent cost analysis without loss of information across all project phases.
Incorporating a hybrid model can significantly enhance a business's ability to manage costs effectively, adapt to changes, and align operational activities with strategic goals. By understanding and integrating the strengths of both bottom-up and top-down costing, businesses can achieve a more comprehensive and effective costing strategy.
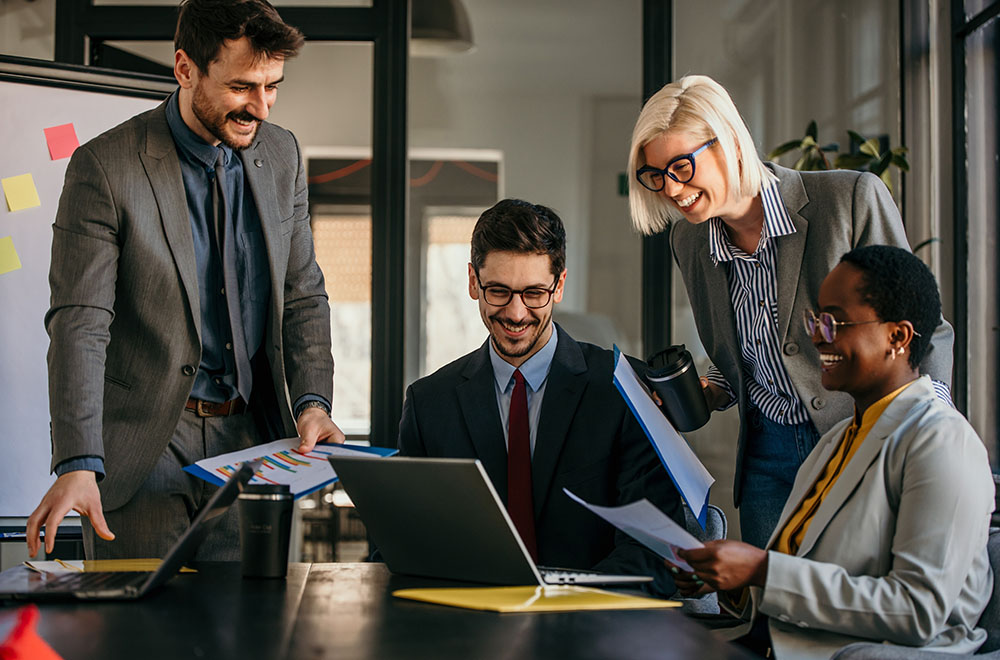
Efficient costing with 4cost
The software and service solutions from 4cost provide you with a maximum of cost transparency at all phases. For improved cost control and increased profitability.
Request a commitment-free presentation now. Our experts will be happy to advise you on the right solutions for your company.