Cost planning: Important terms explained in detail
Three dimensions play a role in project management: deadline, quality and costs. Costs in particular are often a challenge in practice. Exceeding planned budgets is not uncommon. Sound and realistic cost planning is therefore essential for the success of a company. However, in order to be able to grasp the expected total costs of a project or order as accurately as possible, some prerequisites must be met.
This article explains the basic concepts of cost planning in the context of customer-related projects. Detailed cost planning is essential for the management of any project, quotation, production process or work package. It shows which factors affect the total costs and how the individual items can be determined in a targeted manner. In addition, we address the question of how an optimal quotation can be conducted with which a solid pricing for customers is possible. With good cost planning, you are able to significantly minimise the risk of cost overruns and uneconomical projects.
What is cost planning?
The term “cost planning” generally describes an instrument for estimating costs that will be incurred in the future. In a business sense, this can refer to the company as a whole, individual company divisions, products and services. In addition, cost planning is used in project management and in quotation costing to estimate project- or order-related expenses.
When planning customer-related projects or individual orders, the primary goal is to determine and present the expected costs of individual work packages or processes as accurately as possible in advance. On the one hand, this forms the basis of the quotation calculation, and on the other hand, ensures companies that the actual costs incurred do not deviate too much from the original estimate, which would result in uneconomical orders. Cost planning also serves another purpose: it facilitates a target/actual comparison throughout the course of the project and is therefore an important instrument for project control.
Even if cost planning is hardly possible due to a lack in the description of project details, at least a rough estimate of expected project costs must be made. This allows clarification on whether a project is feasible or not. This initial cost estimate is then enhanced and replaced by a detailed calculation during the ongoing project.
Resource planning as a basis for the cost plan
In order to estimate the total costs of a project, the project must first be divided into individual sections (keyword: work breakdown structure). Each of these sections is evaluated individually and the costs of all the subsections are added up. Once you have a precise list of all project tasks as well as the resource plan, the project cost planning can begin. Other planning information (e.g., sequence -and milestone planning), on the other hand, hardly plays a role in cost planning. The following resources and cost types affect the project costs:
- Material: Direct material (raw materials, parts, components), auxiliary materials, consumables, operating materials (valued in acquisition prices or at production costs)
- Personnel: Costs for in-house employees involved in the project (valued in daily or hourly rates)
- Plant, machinery and equipment provided (evaluated at cost price)
- External services: Costs for project-related external services by service providers (evaluated by obtaining quotations)
- Incidental costs: For example, equipment, travel costs, costs of seminar rooms, insurance, etc.
- Capital and interest costs: Relevant for the external pre-financing of project costs
What is unit cost planning?
Direct costs are costs that can be directly and unambiguously assigned to a specific cost unit (in this case: an order or project). These are therefore also referred to as direct costs or direct cost unit costs. The following types of direct costs must be considered in project management:
- Direct material costs: Material needed for the product as the main ingredient
- Direct labour costs: Wages that can be directly attributed to the cost unit
- Special direct costs: Are not allocated to individual products but to orders with similar products (e.g., packaging, transport, commissions)
Individual cost planning is based on the “expected factor quantities” consumed (e.g., costs, labour hours, material quantities). This “factor quantity” is referred too as standards. In order to determine the standards, there are additional possibilities to choose from:
- Parts lists
- Construction drawings
- Estimates based on experience
- Statistical historical values
- External standard values (e.g., consumption average of a certain industry)
In general, some premises should be fulfilled in order to achieve the necessary level of accuracy in planning. For example, fixed planned prices for materials and wages should not be too far away from the market price. If cost prices are used, they should be based on the most competitive offer at that time. In addition, other price components such as freight costs and transport insurance should not be disregarded.
What is total cost planning?
In addition to the directly attributable direct costs, overhead costs naturally also arise in a company during cost planning. These are essentially material overheads, production overheads, administrative overheads and sales overheads. Material overheads are, for example, the operating costs of a warehouse or transport costs. The overhead costs are usually allocated to a product, an order or a project via an overhead rate that was determined in the cost accounting sheet.
If a quotation is to be prepared for a customer, it is indispensable to allocate the overhead costs incurred to the total costs. Only when following this approch a fully cost-covering calculation can be achieved.
It is also sensible to plan for a financial buffer, as this reduces the risk of budget overruns. However, it should be borne in mind that this has a direct impact on the bidding process and makes the project’s profitability appear more negative than it may really is.
What belongs in the quotation costing?
Quotation costing is an extended form of project costing. Various surcharges are added in order to eventually calculate the pricing for the customer. Since these are usually binding offers, an exact clarification and explanation of the order must be made in advance as a base for the order calculation. The requested service must therefore be defined as concretely as possible in order to be able to create a reliable calculation.
The costing of quotations follows a defined structure. It includes the production costs, the cost of goods sold and the proposal price of a project. In the following, we elaborate on the topics that are classically included in an overhead cost estimate.
Material costs
If a product is to be manufactured, the costs for raw materials and components are taken into account. The surcharges for material overheads are also included.
Production costs
All costs for the production of a product are summarised under this category. Overhead surcharges are also included here.
Third-party costs
This includes costs for services provided by subcontractors, for the refinement of products as well as the costs for other services (such as for the conception, the implementation of events or for technical drawings). The basis for this kind of calculation is usually the offer of the subcontractors.
Costs for the companies own contributions and services
This position includes the expenditure for the own staff of the company in hours or in person-days. In most cases, the scope is estimated on the basis of the project plan and calculated using the company’s own hourly rates.
Other costs
These are other project-related expenses that are necessary for service delivery – for example, costs for travel activities, training costs and insurance costs.
Overhead surcharges
The sum of all the topics listed so far represents the manufacturing costs. Surcharges for overhead costs are now added. Classical examples are costs for distribution, shipping, management and administration. Depending on the industry, risk or warranty surcharges are also standard.
Profit mark-up
The sum of production costs and overhead surcharges represents the so-called cost of goods sold. Then the desired profit margin is added.
Discounts
If necessary, surcharges for expected profit reductions (rebates, discounts, etc.) are added to the price. This allows a certain amount of leeway for price negotiations.
Quoted price
If the profit mark-up and mark-ups for price reductions have been added to the prime costs, the result is the final quotation price.
Post-cost calculation makes deviations transparent
Finally, it should be briefly mentioned that a recalculation of all costs is recommended. It shows whether a cost overrun or a cost underrun of the project has occurred. In addition, the post-calculation fulfils an important control function. Transparencies in which areas your planning had weak points are also received. It may be possible that the schedule was not complied with and that more or fewer working hours were incurred than originally planned. Raw material prices may also have risen during the project. Or perhaps you simply used outdated data for the calculation. Especially in the case of high deviations that occur regularly, you should think of systematic errors in the method of your quotation costing. All in all, the target/actual comparison provides information on how you can calculate more accurate, and more realistic offer prices in the future calculations.
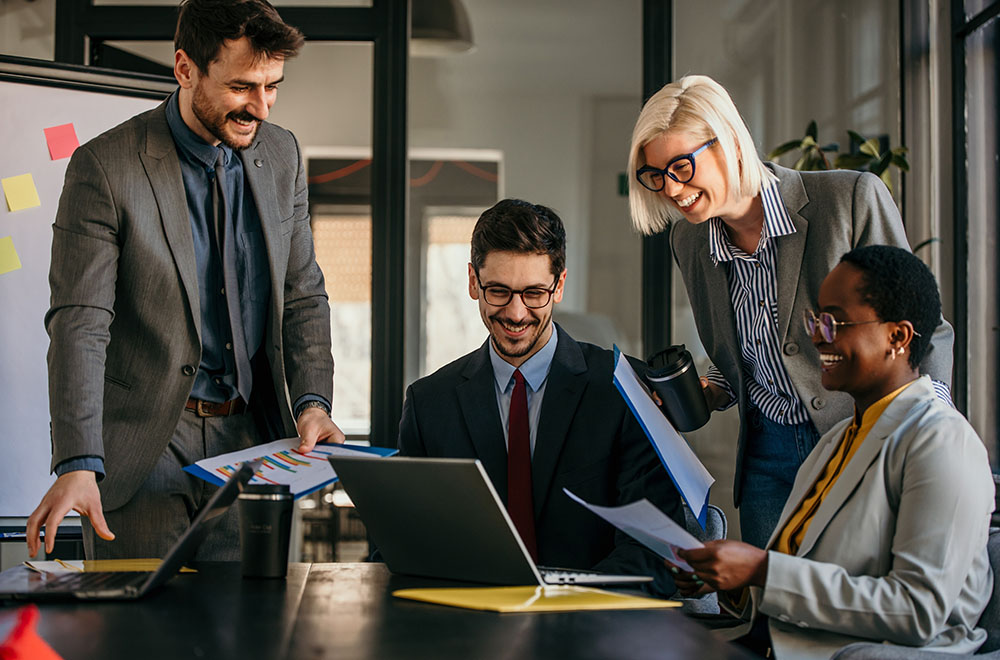
Accurate cost planning with 4cost
The software and service solutions from 4cost provide you with a maximum of cost transparency at all phases. For improved cost control and increased profitability.
Request a commitment-free presentation now. Our experts will be happy to advise you on the right solutions for your company.