ESG costing: Strategies for successful implementation and management
In recent years, Environmental, Social, and Corporate Governance (ESG) factors have become increasingly important for businesses across all industries. ESG refers to the three central factors in measuring the sustainability and societal impact of an investment in a company. Environmental criteria consider how responsibly a company treats nature. Social criteria examine how it manages its relationships with employees, suppliers, and customers as well as its engagement in the community. Corporate governance is about the leadership and supervision of a company, ethical principles, transparency, integrity and compliance with regulations.
As consumers, investors, and regulators place greater emphasis on sustainability and social responsibility, the manufacturing industry finds itself at the forefront of the ESG movement. Manufacturers play a crucial role in the adoption and implementation of ESG practices due to their significant environmental impact, complex supply chains, and influence on local communities. However, embracing ESG comes with its own set of financial challenges and considerations.
This blog post aims to explore the costs of ESG in the manufacturing industry, examining the direct and indirect expenses associated with sustainability initiatives. We will also discuss the potential benefits of ESG adoption and provide strategies for manufacturers to effectively navigate the financial impact of sustainability. By understanding the full scope of ESG costing, manufacturers can make informed decisions and develop a roadmap for a more sustainable and resilient future.
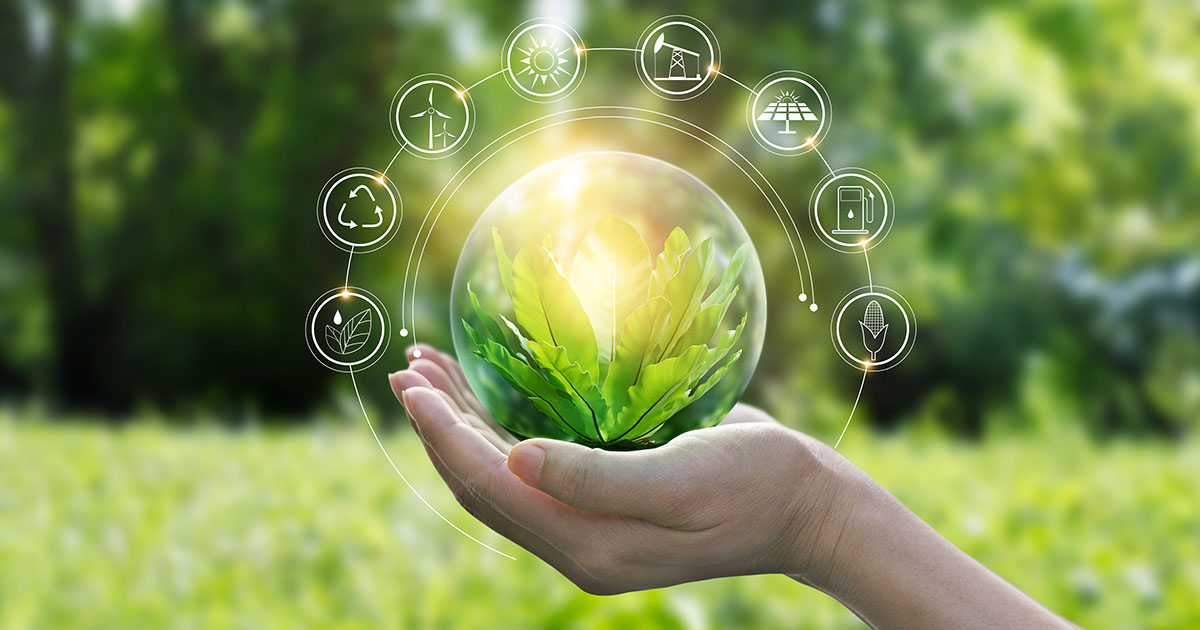
The components of ESG costing
Environmental costs
At the heart of ESG costing lies the environmental component, which is critical for companies that want to operate sustainably. Companies are increasingly required to account for their environmental impact, which includes their carbon footprint, waste management and overall resource consumption. Calculating these costs involves assessing direct operational impacts, such as energy consumption and greenhouse gas emissions, as well as indirect impacts, such as the impact on the life cycle of products and suppliers. By quantifying these aspects, companies can identify areas for improvement, reduce their environmental footprint, and potentially lower associated costs.
Social costs
The social dimension of ESG focuses on a company's relationships with its employees, suppliers, customers, and the communities in which it operates. This includes labour practices, such as fair wages and safe working conditions, community involvement and respect for human rights. Although social costs are less tangible and harder to quantify than environmental costs, they are crucial for maintaining a company's social licence to operate. Companies can assess social costs by evaluating employee turnover rates, community investment initiatives, and compliance with labour laws. The aim is to identify and mitigate risks related to social issues that could have financial consequences, such as boycotts or lawsuits.
Governance costs
Corporate governance relates to the set of practices, policies, and procedures that a company follows in its operations and decision-making processes. This includes the composition and structure of the board of directors, the remuneration of senior management, the audit of financial statements, internal controls, and shareholder rights. Governance costs are associated with maintaining transparency, ethical standards and compliance. Poor governance can lead to significant legal and financial consequences, eroding investor trust and company value. To determine the cost of governance, companies need to review their governance practices, ensuring they align with best practice and legal requirements. Effective governance can prevent fraud, corruption, and other misconduct. As a result, costs associated with litigation, fines, and reputational damage can be avoided.
Direct and indirect costs related to ESG
Adopting ESG practices in the manufacturing industry comes with a range of financial implications. These costs can be categorized into direct and indirect costs, both of which can significantly impact a company's balance sheet.
Direct costs
Investments in sustainable technologies and processes: Manufacturers may need to invest in new, eco-friendly technologies and processes to reduce their environmental footprint. This may include implementing renewable energy systems, such as solar panels or wind turbines, or adopting energy-efficient equipment and machinery. These investments often require substantial financial upfront investment.
Upgrading facilities and equipment to meet ESG standards: To comply with ESG regulations and standards, manufacturers may need to upgrade their existing facilities and equipment. This may involve retrofitting buildings to improve energy efficiency, installing air and water filtration systems, or replacing old equipment with more sustainable alternatives. These upgrades can be costly and require significant resources.
Increased raw material costs for eco-friendly materials: As manufacturers switch to more sustainable practices, they may need to source eco-friendly raw materials and materials. These materials can be more expensive than conventional alternatives, leading to higher production costs. For example, using recycled or biodegradable packaging materials may be more expensive than traditional plastic packaging.
Indirect costs
Cost of compliance and reporting: ESG adoption often involves complying with various regulations and standards, such as carbon emissions reporting or auditing labour practices. Manufacturers may need to invest in new systems and processes to track, monitor, and report on their ESG performance. This may involve hiring additional staff, engaging external auditors, or purchasing specialised software, which can add to the total cost of implementing ESG measures.
Employee education and training: Adopting ESG practices requires a change in corporate culture and employee mindset. Manufacturers may need to invest in training programmes to ensure that their employees have the necessary knowledge and skills to support ESG initiatives. This could include workshops on sustainability best practices, training on new technologies and processes, or communicating the importance of social responsibility.
Potential supply chain disruptions during ESG transition: When manufacturers switch to more sustainable practices, they may experience disruptions in their supply chains. This may be the case if existing suppliers are unable to meet the new ESG standards or if the company needs to find new suppliers that meet its sustainability goals. Disruptions to the supply chain can lead to increased costs, production delays and potential loss of revenue.
While the financial impact of adopting ESG standards can be significant, it is important to consider these costs in the context of the long-term benefits and the growing importance of sustainability in the manufacturing industry. By understanding and effectively managing these costs, manufacturers can position themselves successfully in an increasingly ESG-oriented corporate landscape.
Benefits of ESG adoption in the manufacturing industry
Despite the financial challenges associated with adopting ESG, there are many benefits for manufacturers who adopt sustainable practices. These benefits can help offset the initial costs and create long-term value for the company.
Improved brand reputation and customer loyalty: As consumers become increasingly conscious of the environmental and social impact of the products they purchase, manufacturers that demonstrate a strong commitment to ESG principles can enhance their brand reputation. By showcasing their sustainability efforts and transparently communicating their ESG performance, manufacturers can differentiate themselves from competitors and build customer loyalty. This can lead to increased sales, as customers are more likely to choose products from companies that align with their values.
Improved access to capital from ESG-oriented investors: Investors are increasingly incorporating ESG factors into their decision-making processes. Manufacturers with strong ESG performance can attract capital from sustainability-oriented investors, such as green bonds or ESG-oriented investment funds. This access to capital can provide manufacturers with the financial resources needed to invest in further ESG initiatives and drive long-term growth.
Long-term cost savings through energy efficiency and waste reduction: While the upfront costs of adopting sustainable practices can be significant, manufacturers can achieve long-term cost savings through improved energy efficiency and waste reduction. By investing in energy-efficient technologies and processes, manufacturers can reduce their energy consumption and associated costs. Similarly, by minimising waste and implementing circular economy principles, manufacturers can reduce their raw material and disposal costs. These cost savings can help offset initial investments in ESG initiatives and contribute to a more profitable and sustainable business model.
Increased appeal as an employer: Adopting ESG can increase a company’s appeal in the recruitment of professionals. In recent years, there has been a growing trend of job seekers, particularly among younger generations such as Millennials and Generation Z, who prefer to work for companies that align with their personal values and demonstrate a strong commitment to environmental and social responsibility. By demonstrating their ESG commitment, manufacturing companies can attract top talent who seek purpose-driven work and want to contribute to a more sustainable future.
Steps to implement ESG costing
Implementing ESG costing is a comprehensive process that requires careful planning and commitment. The key steps for a successful implementation are outlined below.
Step 1: Conduct an ESG audit
Assessment: Start by assessing your current environmental, social, and governance practices. Identify areas where your business impacts the environment, your employees, and the community, and how your governance structures are set up.
Data collection: Collect all relevant data, such as energy consumption, waste generation, labour practices, and compliance records. This data will form the basis for your ESG calculations.
Step 2: Setting measurable ESG goals and targets
Target: Based on the results of your audit, set clear and measurable ESG goals that align with your company's mission and values. These objectives should address the key areas of impact and opportunities for improvement identified during the audit.
Benchmarking: Establish benchmarks and KPIs (Key Performance Indicators) to measure your progress towards these goals.
Step 3: Integrating ESG factors into budgeting and financial planning
Financial consideration: Include ESG costs and savings into your financial planning. This can include investments in sustainable resources, costs for reducing emissions, or funds allocated for community programmes.
Decision making: Ensure ESG considerations are part of all major business decisions, from product development to supply chain management.
Step 4: Regular monitoring, reporting, and adjusting
Monitoring and reporting: Develop a system for regularly monitoring and reporting on ESG factors and performance. This may include internal reporting systems or third-party verification.
Continuous improvement: Use the data collected to continuously improve your ESG strategies. Adjust targets and practices as needed based on performance against benchmarks and changing regulations or standards.
Step 5: Employee training and participation
Training: Educate your employees on ESG practices and how they contribute to business objectives. This will ensure that everyone is informed, engaged and motivated.
Engagement: Encourage your employees to get involved in ESG initiatives, such as volunteering, sustainable practices at work, or participating in ESG decisions.
Step 6: Involvement of stakeholders
Communication: Regularly communicate your ESG efforts and achievements to stakeholders, including employees, customers, investors, and the community.
Feedback: To gain different perspectives and improve your ESG strategies, you should seek feedback from your stakeholders.
Step 7: Using technology efficiently
Data management: Use technology solutions to collect, manage and analyse ESG data. This can improve the accuracy of your ESG reporting and the efficiency of your ESG initiatives.
Innovation: Stay abreast of technological advances that can improve your ESG performance, such as renewable energy, waste reduction technologies, or ethical supply chain solutions.
Strategies for managing ESG costs in the manufacturing industry
To effectively manage the financial impact of adopting ESG initiatives, manufacturers can adopt a number of strategies to manage costs and optimise their sustainability efforts.
Step-by-step implementation of ESG initiatives
Rather than trying to transform the entire operation at once, manufacturers can take a phased approach to ESG implementation. By prioritising initiatives according to their potential impact and feasibility, manufacturers can spread costs over time and minimise disruption to business operations. This gradual approach allows for continuous improvement and adaptation as the company gains experience and insights from its ESG efforts.
Collaborating with industry partners and suppliers
Manufacturers can use partnerships and collaborations to share the costs and risks associated with ESG implementation. By working with industry partners, manufacturers can pool resources, share best practices, and develop joint solutions to common sustainability challenges. In addition, working with suppliers to develop more sustainable materials and processes can help reduce costs and ensure a more resilient and responsible supply chain.
Government incentives and grants for sustainable projects
Many governments offer financial incentives and grants to support companies in their sustainability efforts. Manufacturers can take advantage of these opportunities to offset the costs of ESG initiatives. For example, some governments offer tax credits for investments in renewable energy or energy-efficient technologies. Others offer subsidies for research and development of sustainable innovations. By taking advantage of these incentives, manufacturers can reduce the financial burden of ESG adoption and accelerate their sustainability progress.
Integrating ESG into core business strategy and decision-making
To maximise the benefits and minimise the costs of ESG implementation, manufacturers should integrate sustainability considerations into their core business strategy and decision-making processes. This includes aligning ESG goals with business objectives, setting measurable targets, and regularly monitoring and reporting on progress. By integrating ESG into corporate culture and processes, manufacturers can identify opportunities for cost savings, innovation and growth, while minimising the risk of costly mistakes.
Effective cost management is crucial for manufacturers to manage the financial impact of ESG adoption. By applying these strategies and continually refining their approach, manufacturers can optimise their sustainability efforts and create long-term value for their business and stakeholders.
Conclusion
The manufacturing industry is evolving and adapting to the growing importance of sustainability. Adopting ESG is no longer an option, but a necessity. While the financial impact of ESG can be significant and the direct and indirect costs affect a company's bottom line, the long-term benefits of sustainability far outweigh the short-term expenses.
Manufacturers that successfully manage the costs of implementing ESG benefit from a better brand image, stronger customer loyalty, access to new sources of capital, and long-term cost savings through efficiency and waste reduction. Moreover, by integrating ESG into their core business strategy and decision-making processes, manufacturers can reduce risk and improve their overall resilience to global challenges.
However, managing the financial impact of ESG requires careful planning and execution. Manufacturers must weigh the costs and benefits of sustainability initiatives and prioritise those that will bring the greatest value to their business and stakeholders. By employing strategies such as gradual implementation, collaboration with industry partners, seeking government funding, and integrating ESG into the core business, manufacturers can optimise their sustainability efforts and minimise the financial burden.
The importance of ESG will continue to grow as the manufacturing industry evolves. Companies that embrace sustainability and effectively manage the associated costs will be well-positioned to thrive in an increasingly ESG-focused business environment. By taking a proactive and strategic approach to ESG, manufacturers can not only contribute to a more sustainable future but also ensure their own long-term success and competitiveness.
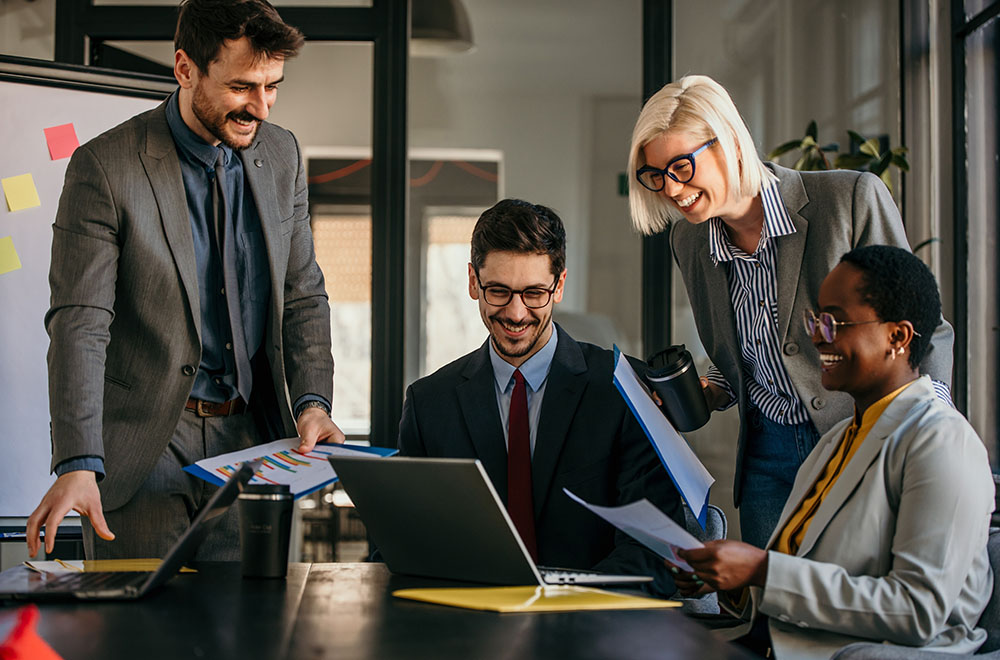
Reliably calculate ESG with 4cost
The software and service solutions from 4cost provide you with a maximum of cost transparency at all phases. For improved cost control and increased profitability.
Request a commitment-free presentation now. Our experts will be happy to advise you on the right solutions for your company.