Bewertung der Zielkosten eines mechatronischen Laser-Messsystems in der Konzeptphase
Früheste Kostenschätzung mit 4cost im Design-Workshop mit maximaler Abweichung von 4 % (Serie)
Ausgangssituation & Aufgabe
- Produktneuentwicklung ist geplant
- Erste Konzepte und Ideen sind vorhanden
- Zu welchen Kosten können wir herstellen?
- Bei welchen Herstellkosten und wann stellt sich der Break-Even-Point ein?
Vorgehensweise
- Ideenworkshop mit Kostenbewertung der einzelnen Konzepte
- Grobe Strukturentwicklung (Stückliste)
- Bewertung der einzelnen Komponenten und Baugruppen
- Bewertung der Montage und Testaufwände
- Simulation und Untersuchung von verschiedenen Szenarien
Ergebnisse
- Klare Herausarbeitung von Zielkosten
- Nach zwei Jahren wurde das Produkt gelauncht
- Kostenabweichung zwischen frühester Schätzung und tatsächlichen Herstellkosten bei ca. 4 %
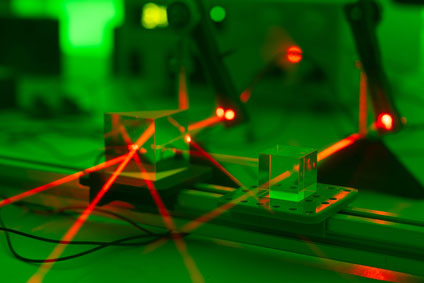
Parametrische Bewertung von Werkzeugen und Vorrichtungen
4cost identifiziert Kostenpotenzial von 30 %, unterstützt bei Verhandlung und realisiert 25 % Kostenreduktion
Ausgangssituation & Aufgabe
- Ein Lieferant wurde gebeten ein erstes ROM abzugeben
- Das Management wünscht Klarheit über das „Value-for-money“
- Interne Abschätzungen beruhen auf „Expertenwissen“ ohne jegliche Transparenz
Vorgehensweise
- Aus den technischen Beschreibungen (grobes Lastenheft) wird eine parametrische Kalkulation erstellt
- Aufbau einer Grobstruktur
- Parametrische Bewertung der einzelnen Komponenten und Baugruppen
- Validierung der Montage und Testaufwände
Ergebnisse
- Das Should Costing von 4cost weist ein Delta von 30 % zum ROM auf
- Mit dem technischen Verhandlungssupport von 4cost wird eine Kostenreduktion von 25 % erreicht
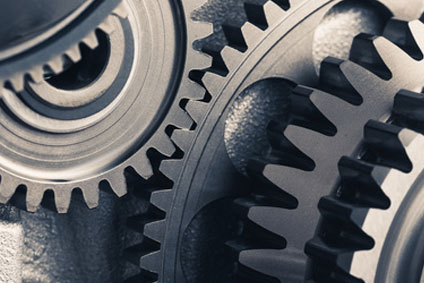
Business-Case-Entscheidung für eine automatische Kastensortieranalage
4cost identifiziert Kostensenkungspotenzial von 29 % bei Standardisierung
Ausgangssituation & Aufgabe
- Ermittlung der Investitionskosten
- Berechnung des Break-Even-Points gegenüber der halbautomatischen Lösung
- Ermittlung von verschiedenen Varianten und Dimensionen
- Bestimmung des Reduktionspotenzials bei Standardisierung
- Ermittlung der Einmalkosten (insbesondere Entwicklungs- und Programmieraufwände)
Vorgehensweise
- Technische Analyse der bestehenden Spezifikationen
- Kostenbewertung des bestehenden Grobkonzeptes
- Prozessaufnahme der aktuellen Situation
- Durchführung von Kostenworkshops mit gleichzeitiger Kostenbewertung alternativer Lösungsmöglichkeiten
- Ausarbeitung der Entscheidungsvorlage
Ergebnisse
- Als Projektauftrag kein Break-Even-Point erreichbar
- Bei Standardisierung: Kostensenkungspotenzial von 29 % (Material, Fertigung) möglich
- Business Case ab einer Stückzahl von sieben Anlagen positiv darstellbar
- Alternative Lösungskonzepte mit Bewertung des Umsetzungsaufwandes
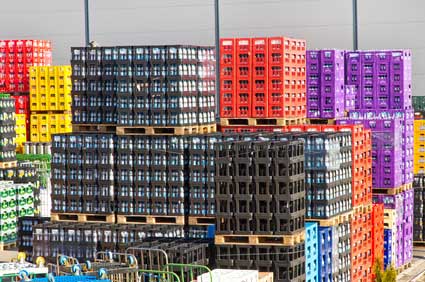
Kostenbewertung einer modifizierten Faserverarbeitungsanlage bei Auslagerung in ein Niedriglohnland
Kostenpotenziale von 15 % im Engineering und 19 % in Sourcing-Strategie nach 4cost-Analyse
Ausgangssituation & Aufgabe
- Vorgängermodell vorhanden
- Jahresabsatzmengen und Märkte vom Vertrieb vorgegeben
- Nur grobe Vorstellung eines erzielbaren Zielpreises
Vorgehensweise
- Kostenbewertung der bestehenden Anlage
- Definition der Änderungen (Delta-Methode)
- Kostenbewertung der Adaptionen
- Untersuchung verschiedener Sourcing-Strategien
- Bewertung von verschiedenen Baugruppenstrukturen bezüglich Fertigung, Logistik, Vor- und Endmontage für verschiedene Länder
- Berücksichtigung von zehn Jahren Projektlaufzeit inklusive Inflation/Kostensteigerung
Ergebnisse
- Klare Herausarbeitung eines Zielpreises
- Kostenpotenziale aus dem Engineering in Höhe von 15 % identifiziert
- Kostenpotenziale aus der Sourcing-Strategie von über 19 % identifiziert
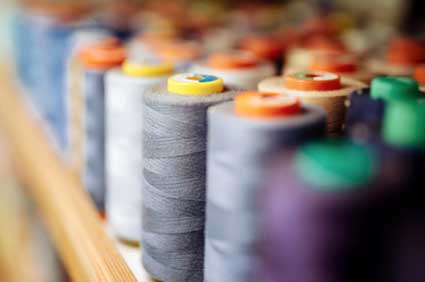
Vereinheitlichung des Kalkulationsschemas und Einführung einer softwaregestützten Kalkulationsmethode
Implementierung einer homogenen Kalkulationslandschaft in zehn Wochen umgesetzt
Ausgangssituation & Aufgabe
- Heterogene Kalkulationslandschaft
- Kein einheitliches Kalkulationsschema und keine einheitliche Methodik
- Unterschiedliche Excel-basierte Lösungen
- Daten und Know-how nicht zentral zugängig
- Wenig Transparenz
Vorgehensweise
- IST-Analyse und Anforderungskonzept
- Erstellung Lasten- und Pflichtenheft für softwaregestützte Kalkulation
- Anpassungen an Software und Test
- Implementation
- Pilotphase
- Produktschulung
- Rollout
Ergebnisse
- Implementierung einer homogenen Kalkulationslandschaft in zehn Wochen umgesetzt
- Vereinheitlichung von Kalkulationsschema und -methodik
- Transparente, nachvollziehbare Kalkulationen
- Zentrale Daten und Dateiverwaltung mit Berechtigungskonzept
- Gebündeltes Know-how
- Einheitliches Reporting
- Detailkalkulation um 23 % schneller geworden
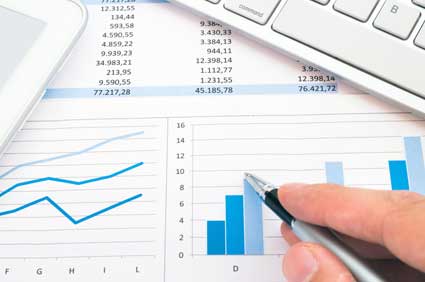